Introduction
High-visibility mechanic gloves featuring goatskin leather palms, para-aramid lining, and breathable fourchette inserts between fingers. These durable gloves moreover offer ANSI Level A3 wear resistance.
Have you overly read the product unravelment for safety gloves and wondered what exactly the glove manufacturer is trying to communicate? With all this “technical glove jargon,” how do you know which safety gloves offer the right level of protection for workers without inhibiting glove performance or comfort? And with myriad safety glove options misogynist on the market, where do you plane start?
You start by bridging the information gap to proceeds an understanding of what goes into manufacturing safety gloves, and the complementary features that influence their performance. In short, you start by reading this guide!
Wearing the right safety gloves—comfortable, correctly sized, and engineered with the right materials—can protect a wearer’s hands versus workplace hazards, lamister potentially life-altering injuries. This is why, we’ve washed-up the legwork for you and created this comprehensive guide with key information on safety gloves. Reading this guide will goody you in making an informed visualization when choosing the next safety gloves for your workers.
To make it easy for the readers, we’ve divided this Glove 101 guide into sections that will imbricate the pursuit topics:
Glove Categories
Jump To SectionGlove Components
Jump To SectionGlove Additives & Treatments
Jump To SectionLet’s begin!

Before we swoop into the specific components of safety gloves, let’s first squint at the fundamental characteristics and construction methods that help categorize these gloves.
There are five main types of work gloves:
Each glove type offers various benefits and features that make them the largest option for specific tasks and hazards. However, they each have their limitations that moreover need to be considered surpassing choosing those best-suited in your work environment.
The table unelevated provides a quick comparative summary of the defining characteristics and limitations of each type of work glove. Later, we will discuss each of them in detail.
Glove Types
Glove Shell Construction
Features and Attributes
Limitations
Leather
Cut pieces are sewn together (has seams)
Common leathers: cow, sheep, goat, pig, horse, buffalo, deer, elk
- Highly durable
- High wear resistance
- Naturally flame resistant
- Less dexterous than string knit
- Least cost-effective when compared to others
String knit
Seamless knit
Common fibers: cotton, nylon, polyester, HPPE, para-aramid
- High dexterity
- High breathability
- Engineered yarns can offer several hazard protections
- Lower tautness than leather
Mechanics
Layers of variegated materials
- Cut and sewn
- High dexterity
- Variety of protection offerings
- Zoned protection
- Less dexterous than string knit
- Less durable than leather
Chemical
Nitrile, Neoprene, Latex, PVC
- Resists liquid and chemical penetration
- Can resist chemical degradation
- Provides limited range of mechanical protection
Disposable
Nitrile, Latex, polyethylene
- Prevents navigate contamination
- Offers the lowest durability
Most safety gloves are either leather or string knit, or a combination of the two (mechanics). Other gloves include chemical and removable gloves. Let’s take a closer squint at their unique construction styles, and key features and attributes.
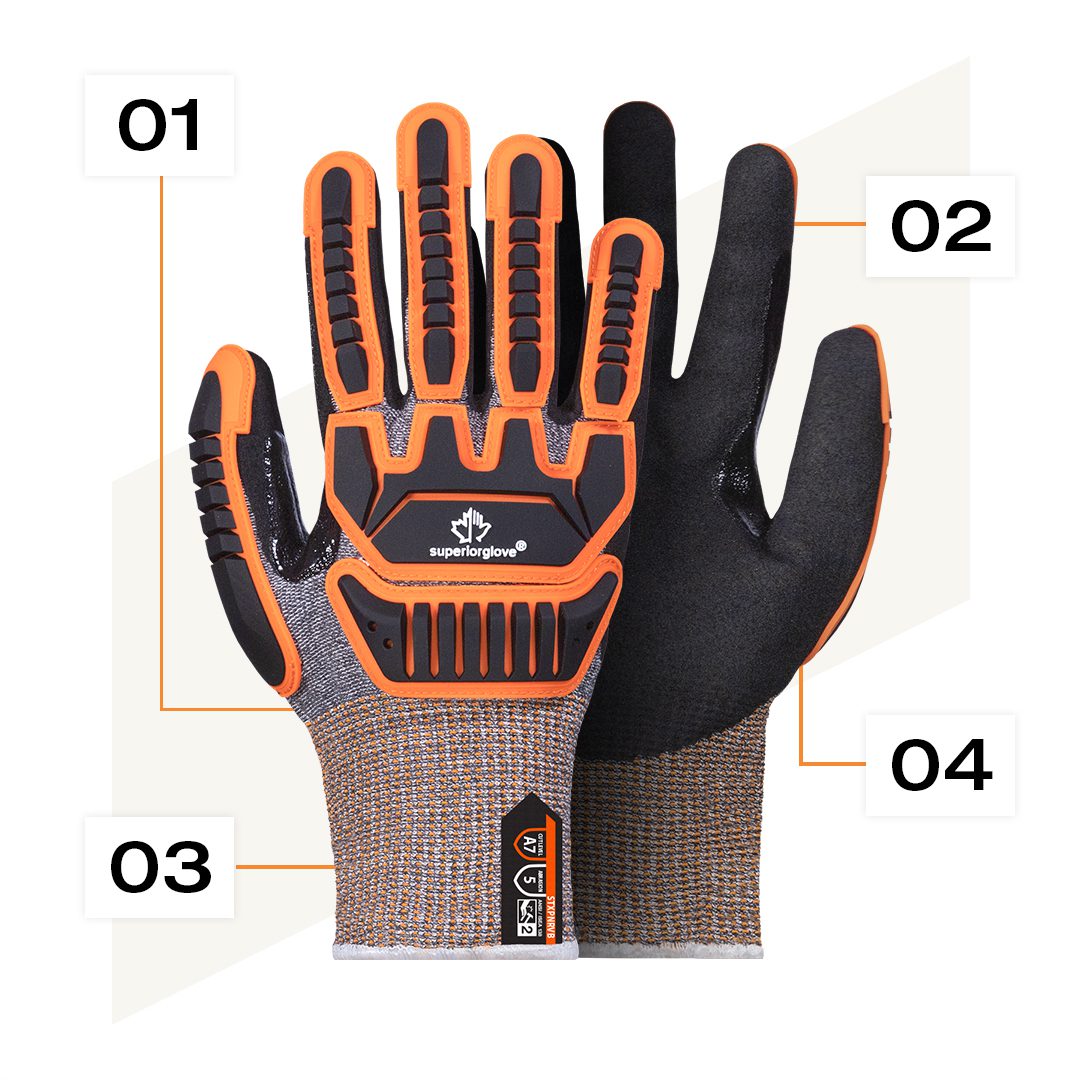
Seamless knit style describes all string knit gloves that are knitted on a hand form using will-less glove knitting machines. During the process, there is no point at which the yarns have to be sewn together—hence, they are seamless. A goody of having no seams is that it improves glove strength by removing stress points where they can be ripped. Flipside wholesomeness of this construction style is that in using yarn (as opposed to leather), the finished form is increasingly dexterous, softer, and pliable.
Knitting it virtually a hand form moreover allows glove manufacturers to integrate ergonomic considerations, like the curves of the fingers, which makes these gloves increasingly well-appointed to wear. It is moreover a increasingly cost-effective and quicker method compared to the cut-and-sew style used in the manufacturing of leather and mechanics gloves, which we will discuss next.
Leather and mechanics gloves are manufactured using the cut-and-sew method. What this substantially ways is that variegated pieces of material are cut out and then stitched together to manufacture these safety gloves. An wholesomeness of this style is that it allows glove manufacturers to unzip variegated sizing requirements increasingly easily. But stitching pieces of materials together moreover ways that these gloves will have seams and impact the finger and dexterity of these gloves.
How variegated pieces are stitched together in a cut-and-sew construction style is unswayable by the glove pattern used. And when we say pattern, it’s the way the fingers and other pieces of the material are attached.
Let’s explore these patterns.
Hover to learn increasingly well-nigh the variegated patterns.
Gunn Cut
- Seamless back
- One “gunn” seam at the wiring of the two middle fingers facing the palm
- Seam in a natural hand ruckle allows fingers to hands bend
- Seam in a removed zone reduces glove wear out
- Most worldwide type of pattern
Clute Cut
- Individual strips of leather sewn together
- Three long seams at the when of the hand
- More unravel points modernize dexterity and range of motion
- Old pattern and not wontedly used
Fourchettes
- Individual strips of fabric that go up the when of the hand and sewn between the fingers
- Seamless palm diamond eliminates wear points
- Inserts between the fingers uplift flexibility and comfort
Straight Thumb
- Thumb sewn straight up – parallel to the other fingers
- Fast to sew and easiest to attach
- Most economical choice
Wing Thumb
- Thumb sewn on completely unappetizing to the side of the glove like a wing
- Fast to sew
- Cost-effective
Keystone Thumb
- Thumb sewn increasingly onto the palm side
- Harder to nail than a wing thumb
- Offers largest ergonomics than wing and straight
Essentially, when constructing leather gloves, the goal is to unzip durability, dexterity, and maintain a sense of feel. And, when constructing mechanics gloves, the goody of this method allows for zoned or targeted protection in areas that require it most.
Another full-length you might have to consider when selecting safety gloves is mitten styles.
There are various styles of cuffs to protect and support your workers’ wrists and stovepipe on the job. For safety and ease of use, it is important to ensure that the glove cuffs are towardly for the task at hand.
GAUNTLET
SAFETY CUFF
HOOK AND LOOP (VELCRO)
ADJUSTABLE PULL STRAP
KNIT WRIST

Leather gloves are highly durable, made with tanned hides of various animals and are a popular nomination for tasks that require abrasion, heat, and fire resistance. Liners can be sewn into leather gloves to offer protection from spare hazards, and other additives and treatments can moreover be integrated to enhance glove performance.
Because leather is a natural material, it softens over time to conform to the hand’s shape. This adds to dexterity and comfort. But not all leather grains are created equal. The part of the animal’s soul the hibernate comes from contributes to leather’s overall thickness, feel, dexterity, durability, and comfort. We will discuss this in increasingly detail in the next section.
Note: The only mechanical protection that leather gloves really provide is wear resistance. While thicker and increasingly undermining hides may moreover offer a stratum of cut and puncture protection—it is nominal. This is considering leather is just skin, and skin inherently offers scrutinizingly no cut or puncture resistance. For this reason, some leather gloves are paired with other engineered materials to enhance protection.
Thanks to engineered yarn, string knit gloves can offer protection from a variety of hazards. Engineered yarns incorporate the benefits of two or increasingly fibers to make them an plane stronger yarn. This moreover allows us to integrate higher levels of protection without compromising repletion or dexterity. Like leather, other additives and treatments can moreover be integrated into string knit gloves to enhance performance. Remoter subtitle of the materials used for string knit gloves will be discussed in the next section under glove shell materials.
Another important factor to consider for knit gloves is the glove’s gauge. Glove gauge, which is unquestionably the gauge of the yarn (i.e., string) used to make the glove, typically ranges from 7- to 21-gauge. Lower gauge gloves are thicker and offer increasingly cushioning and durability, while higher gauge gloves are thinner and increasingly dexterous but not as durable. No one gauge is largest than the other. It all depends on the tasks and hazards for which they’re needed. A increasingly in-depth discussion on glove gauges will be covered under glove materials, later in this guide.
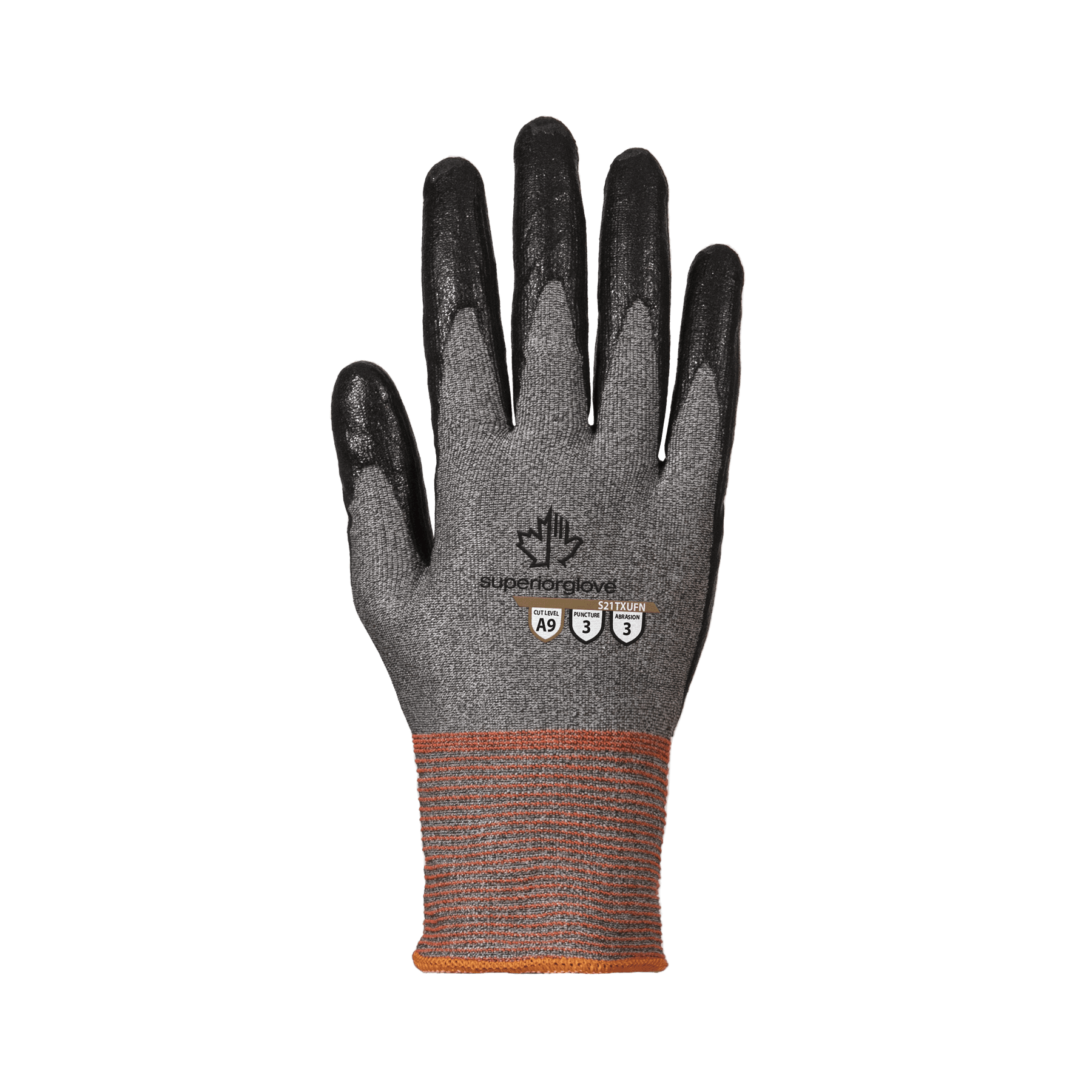

Mechanics gloves are substantially variegated layers of materials (natural or synthetic) sewn together to make gloves. This construction method allows us to integrate zoned protection. What this ways is that protection can be localized to glove areas where hands are at upper risk of injury. Flipside wholesomeness of mechanics gloves is that there is a wider variety of material options that can be sewn onto the gloves that would otherwise be difficult to incorporate in other types of gloves.
Chemical gloves are designed to repel liquids and fluids. The outer shell of chemical gloves is fully coated to resist penetration and soak through of liquids, as well as to resist chemical degradation.
Chemical gloves can be supported or unsupported. An easy way to understand is to think of it as lined or unlined. A lining that supports the glove acts like a skeleton for the glove to maintain its shape, plane without a hand in it. On the other hand, an unsupported glove cannot alimony its shape without a hand wearing it. Cotton and nylon are the two most worldwide materials used as liners for chemical gloves. Less often, you will see high-strength fibers like para-aramid or HPPE stuff used as well. Essentially, the lining adds to the gloves comfort, durability, and ease of donning and doffing gloves.
The weightier way to shop for these gloves is to identify the chemical you’re handling and match it to the glove material that resists that chemical. For this, you can ask an expert or consult your chemical SDS (safety data sheet).
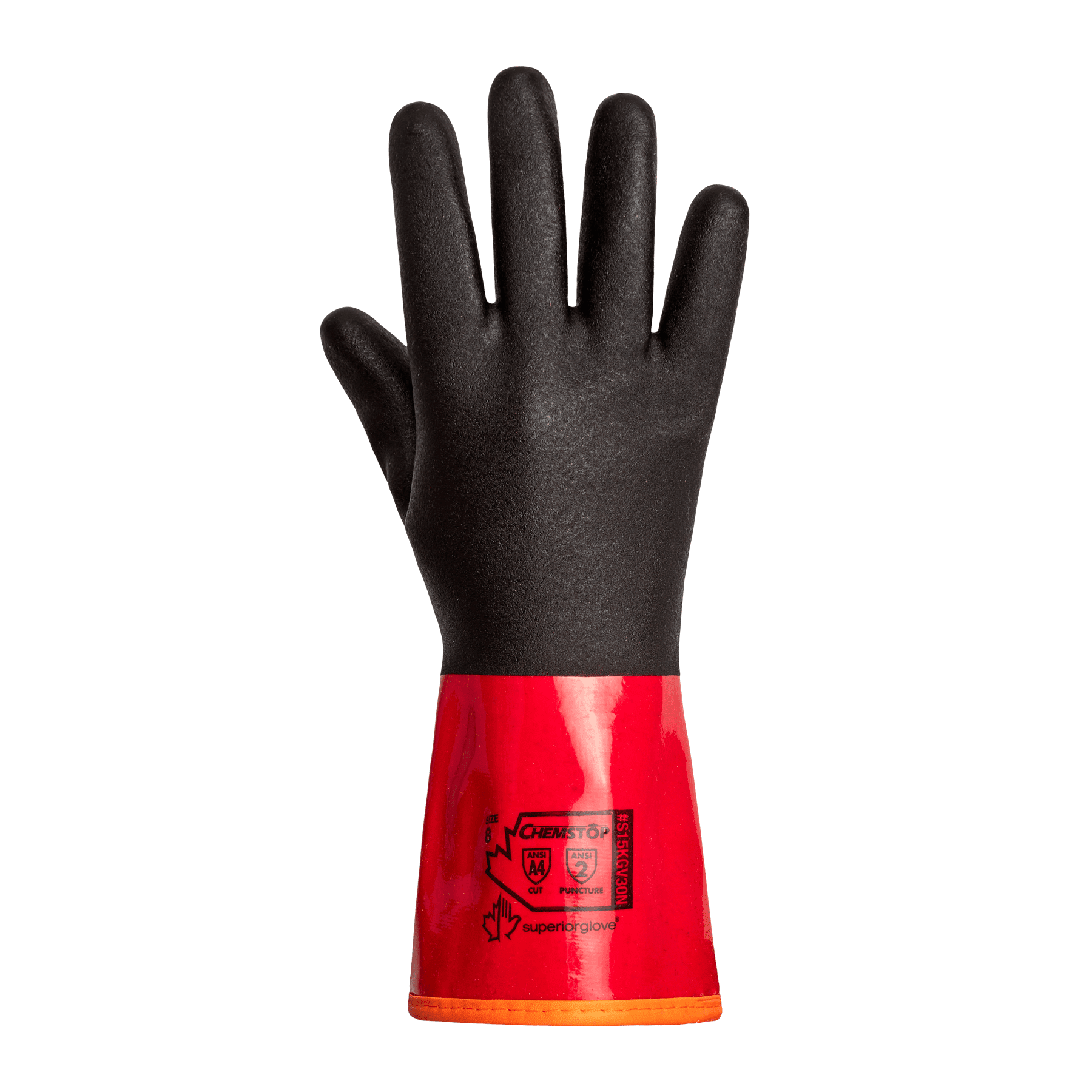

Disposable gloves are primarily used in the supplies and health industry to prevent product contamination of bodily fluids, bacteria, etc. They are wontedly made with nitrile, and sometimes, made with latex (though latex poses the risk of allergic reactions).
Further discussion on features and nature of materials used to manufacture chemical and removable gloves will be covered in the glove coatings section, later in this guide.

Now that we have a vital understanding of the types of safety gloves, the next step is to unravel them lanugo to their plug-in components and see how each influences protection levels, dexterity, and comfort. This requires a deeper understanding of:
The glove shell, or increasingly specifically, the glove shell material, is considered the foundation of all safety gloves. It is the cadre frame that is built upon by incorporating additives and other treatments to remoter enhance glove performance and comfort.
Glove shell materials for most glove types (leather, string knit, and mechanics) can substantially be divided into two major categories: leather and knitted yarn. Materials used for other gloves (chemical and disposable) will be discussed later in this guide under glove coatings.
Grain or split leather? Gloves made with cow, sheep, goat, or flipside hide? How do you segregate between all these options?
The wide variety of options misogynist for leather gloves doesn’t unchangingly make it easy to segregate from. By understanding the key nature and the differences between each type, it can help you make an educated decision.
As noted earlier, leather offers upper tautness and wear resistance and nominal cut and puncture resistance. But not all leather grains are created equal. When choosing leather gloves for specific tasks, it is important to pay sustentation to:
Belly
Economic (good)
Leather cut from the vitals is less durable and often used for economy grade gloves and trims
Back
Medial (better)
Leather cut from when is less optimal than shoulder, but still of upper quality. This is the most cost-effective option and makes up for the zillion of material used in manufacturing safety gloves
Shoulder
Premium (best)
Leather cut from the shoulder offers the greatest tautness and is the most optimal nomination for gloves
In animals that have a thick hibernate like cow and buffalo, leather can be separated between the upper “top grain” and the lower “split” leather.
Grain
Split (Or Suede)
It is moreover important to note that leather harvesting is a byproduct of supplies production. And the quality of leather directly impacts the forfeit of the gloves.
Cow leather is the most worldwide type of leather used for safety gloves and offers high-abrasion resistance. Goat is a tropical second, due to its soft and supple finger and upper dexterity. Other leather types offer varying levels of durability, dexterity, and wear resistance. A quick overview of each type of leather is listed below.
As you notice, when selecting between the variegated types of leathers, the key tradeoff is between tautness and dexterity—how rugged the hibernate is versus how supple it is. And choosing the right safety gloves depends on the task you’re using the gloves for. For instance, tasks that require a greater sense of motion or dexterity, elk skin, deerskin, or goatskin should be the nomination of leather for those gloves. For tasks where there is a upper risk of arc flash, a increasingly rugged material like cow split, horse, or buffalo will offer the necessary protection. Liners are usually sewn into leather gloves to offer spare protection from hazards, and other additives and treatments can moreover be integrated to enhance glove performance. To learn increasingly well-nigh hazard-specific materials, additives, and treatments used to enhance glove’s mechanical protection, trammels out our wares on understanding hazards here.
Let’s take a quick overdue the scenes squint at how yarns are engineered. This will help understand how variegated gloves materials tousle together to enhance glove performance.
All knitted gloves start off as fibers, whether natural or synthetic. These fibers are then either combed, melted, or engineered into yarns. From there, various yarns are spun together using a yarn spinning machine onto a spool (cylindrical device on which thread can be wound). The spools of yarn are then unfluctuating to flipside machine that twists and knits the gloves.
The fundamental yarn materials used in manufacturing safety gloves include:
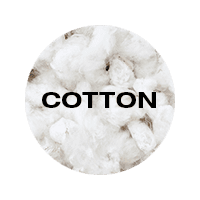
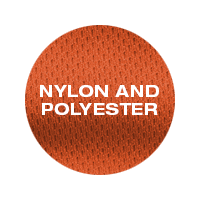
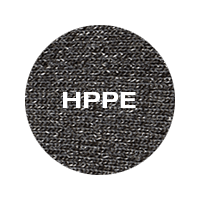

Yarn Type
Features and Attributes
Limitations
Cotton
- Natural fiber
- Very soft and comfortable
- Naturally heat resistant
- Moisture traction properties
Cotton is primarily used in gloves as a liner for comfort
- Not as strong as synthetic fibers
Nylon and Polyester
- Soft and comfortable
- Offers largest tautness and stretch quite well compared to natural fibers
- Cost effective
Nylon and polyester are primarily used in safety gloves as a liner for comfort
- Thermoplastic: melts under heat
HPPE
- High-strength synthetic fiber
- Softer and potation to wear
- More dexterous and flexible than para-aramid
As a high-strength fiber, HPPE offers some stratum of mechanical protection on its own versus cut and puncture hazards
- Thermoplastic: melts under heat
Para-aramid
- High-strength synthetic fiber
- Natural flame and heat resistance
As a high-strength fiber, para-aramid offers some stratum of mechanical protection on its own versus cut and puncture hazards
- Dense webbing compared to HPPE is rougher and warmer to wear
- Less dexterous and flexible than HPPE
- Lower tactile finger compared to HPPE
Additional materials are usually engineered into the supra primary materials for mechanical protection and other benefits, including cut, puncture, flame, heat, dexterity, and comfort. Other additives and treatments can moreover be integrated to enhance glove performance. However, these spare materials do not make up the majority of the glove and are widow to complement the protection workers need for specific hazards. To learn increasingly well-nigh hazard-specific materials, additives, and treatments used to enhance glove’s mechanical protection, trammels out our wares on understanding hazards here.
Gauge is specified as the number of stitches included in each inch of yarn. As the number of stitches increase, so does the gauge. Note that although gauge refers to the yarn, it’s worldwide to hear it tabbed glove gauge. This has the same meaning and is a shorthand way of referring to the thickness or thinness of a glove.
You might think that lower-gauge equals lighter and higher-gauge equals heavier—but in fact, the opposite is true. Lower-gauge gloves are thicker and less dexterous, while higher-gauge gloves are lighter and offer increasingly dexterity.
However, no one gauge is largest than the other. It all depends on the tasks and hazards for which they’re needed. For instance, if comparing a 7-gauge glove to a 21-gauge glove, the 7 gauge will be less dexterous, considering it’s less flexible and has a lower tactile feel. If fine motor skill is needed, this is an issue. But, if the task requires heavy lifting that includes sharp and undermining objects, then workers might prefer a thicker glove as it offers increased cushioning and durability. Refer to the orchestration unelevated for a quick reference of glove gauge versus glove performance.
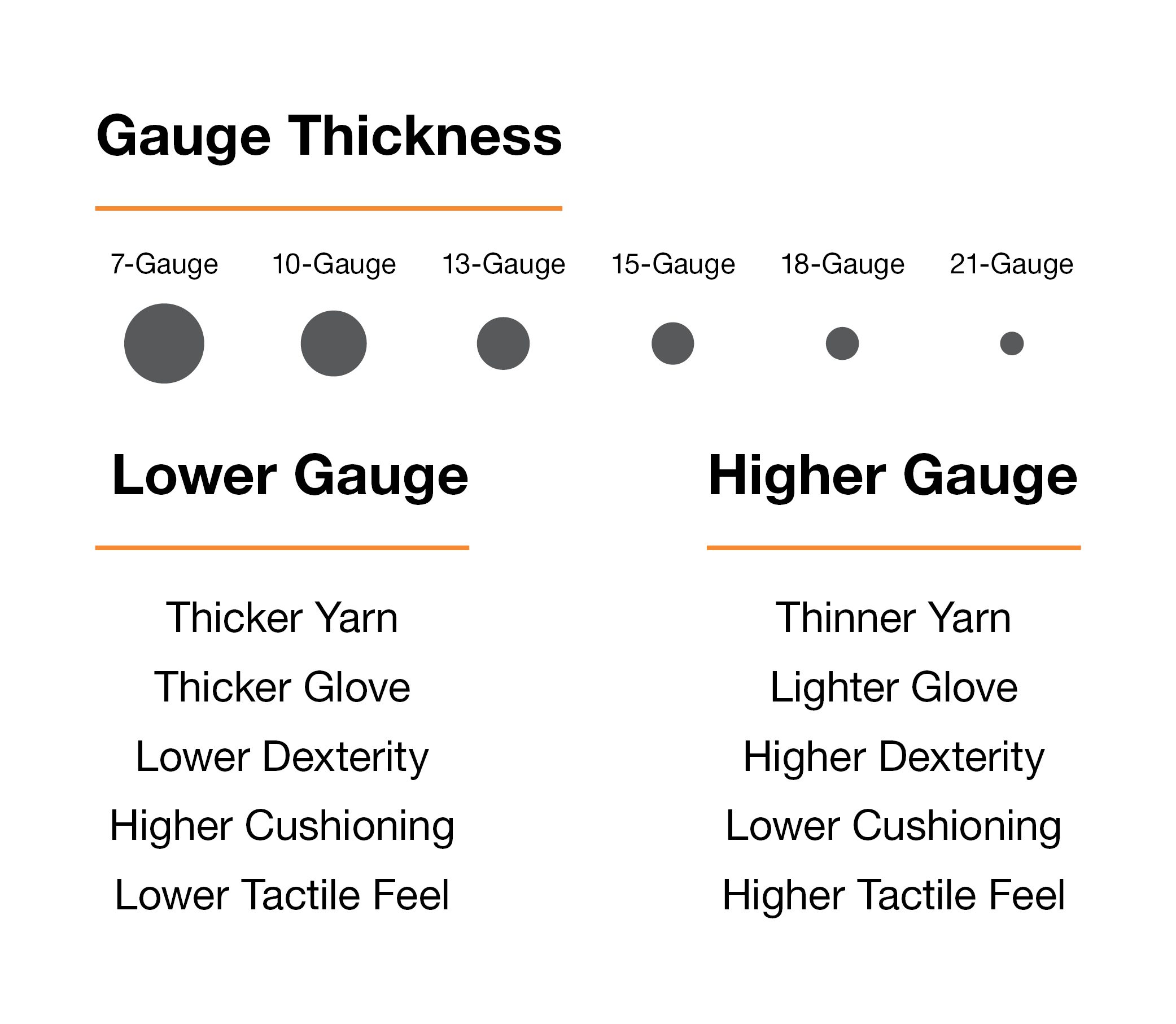

Additive and treatments are incorporated into safety gloves to complement existing features or add features that may be missing. These can include:
Palm coatings serve as an spare layer of protection on safety gloves that can be tailored for specific tasks and work conditions. When it comes to mechanical protection, all palm coatings offer some stratum of wear and puncture resistance (depending on the thickness of the coating). Palm coatings moreover contribute to improved grip and durability.
We’ve listed unelevated the most popular coating materials with their benefits and limitations to help guide you better.

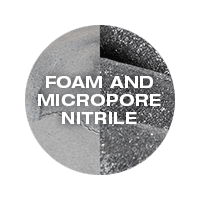





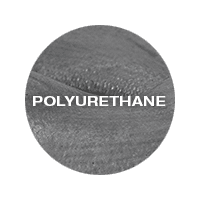
Coating Material
Features and Attributes
Limitations
Flat Nitrile
Nitrile is the most versatile palm coating. It offers the weightier wet/oil grip compared to others. This is expressly true with foam and micropore nitrile. It is highly durable, increasingly than PU (Polyurethane) but less than latex. Unappetizing nitrile is moreover tougher than the porous foam and micropore nitrile.
Limited dexterity and stiffen up in unprepossessed temperatures.
Foam and Micropore Nitrile
Foam and micropore nitrile are made by introducing air frothing into the nitrile mixture. This creates a space where liquids can escape to when working with wet or oily surfaces.
Foam and micropore nitrile are very similar, in that they offer spanking-new wet/oil grip, but unzip results differently. While foam nitrile absorbs and disperses liquid in the palm for improved grip, micropore acts like suction cups to enhance grip.
Limited dexterity and stiffen up in unprepossessed temperatures.
Latex
Latex is very economical and offers strong dry grip. Considering it is a natural rubber, it has a little increasingly stretch to it when compared to nitrile and offers largest tautness and puncture resistance.
Latex does not have very strong wet grip and stiffens up in unprepossessed temperatures. It is moreover very susceptible to natural solvents (organic solvents), so it degrades overtime as it dries out and is prone to cracking.
Crinkle Latex
Crinkle latex has a larger surface zone on the palm compared to unappetizing latex. This helps modernize the grip plane more, plane wet grip, considering gives the water some place to go. As a natural rubber, it is very durable and offers good puncture resistance.
Even though crinkle latex helps modernize wet grip, overall it is largest for dry grip applications. Crinkle latex moreover stiffen up in unprepossessed temperatures.
Neoprene
Neoprene is not as worldwide and primarily used for its natural upper flame resistance. For instance, neoprene palm coating is used in string knit gloves to unzip arc wink protection.
Less durable and poorer oil/wet grip than nitrile.
PVC
PVC offers natural resistance to a lot of chemicals and is platonic for working in extremely unprepossessed temperatures—it doesn’t stiffen up.
PVC does not have very good tactility and is prone to tearing.
Silicone
Silicone is quite unique. It offers upper heat resistance as it has a very upper melting point, and good wear and puncture resistance. It is moreover very wrapper resistant.
Silicon offers poor wet grip. It moreover contaminates the surface you’re working on, which affects the quality of finished products.
Polyurethane (PU)
PU coatings offer a upper level of dexterity and tactility. PU is the most wontedly used material for non-marring gloves. There are two types of PU coatings: water-based PU and solvent-based PU.
PU coatings are less durable and offer poor wet grip and stereotype dry grip when compared to other coatings. They moreover stiffen up and one-liner in unprepossessed temperatures.
The two types of PU:
Water-Based PU
Thinner, tactile, and offers a higher level of dexterity than solvent-based PU.
Not as durable as solvent-based PU.
Solvent-Based PU
More durable and tackier than water-based PU.
Less tactile than water-based PU.
The same palm coating materials listed whilom serves as the glove shell for chemical and removable gloves, in which the unshortened glove is primarily synthetic of that coating. Let’s review the key considerations to alimony in mind when selecting materials for chemical and removable gloves one increasingly time.
Glove liners serve as an spare layer to enhance comfort, warmth, or mechanical protection for the wearer, depending on the task and work conditions. Read on to learn how.
When we say glove insulation, we’re substantially talking well-nigh preventing the external temperature from interfering with the hand’s temperature—also known as thermal control. And we use variegated materials to unzip this.
For gloves meant for shoulder or summer season, the lining is made of materials that resist heat i.e., materials resist transpiration in temperatures and prevent the loss of tomfool air trapped inside the gloves. A good example of this type of material is para-aramid (refer to the section on glove shell materials to review the features, attributes, and limitations of variegated glove materials).
For winter gloves, we use materials that indulge to trap in as much warm air as possible. And the increasingly air it traps, the warmer the glove will be. The two most worldwide glove liners used to alimony workers’ hands warm in the winter seasons include:


Thinsulate is a breathable and moisture-resistant insulator that offers optimum warmth in unprepossessed environments. It is constructive at trapping air and keeping hands warm while permitting moisture to escape. Thinsulate
liners are largest for warmth when compared to fleece, but it is moreover increasingly costly.
The level of Thinsulate used for lining is measured in GSM (grams per square meter). This describes how much insulation is widow to the gloves (the thickness of the liner). Generally, 100 GSM is sufficient to alimony hands warm without losing on dexterity for most winter temperatures, lanugo to -25°C. 200 GSM lining is used for heavy-duty winter safety gloves, but this moreover makes the gloves thicker and heavier, so you’re moreover losing some level of dexterity.
Acrylic or fleece liners are a good starting point as the temperatures are just starting to drop. It is one of the most worldwide lightweight options that is warmer than cotton or foam lining and less unwieldy than other insulations. Gloves with fleece liners could moreover be sufficient for indoor workspaces that are kept at potation temperatures.
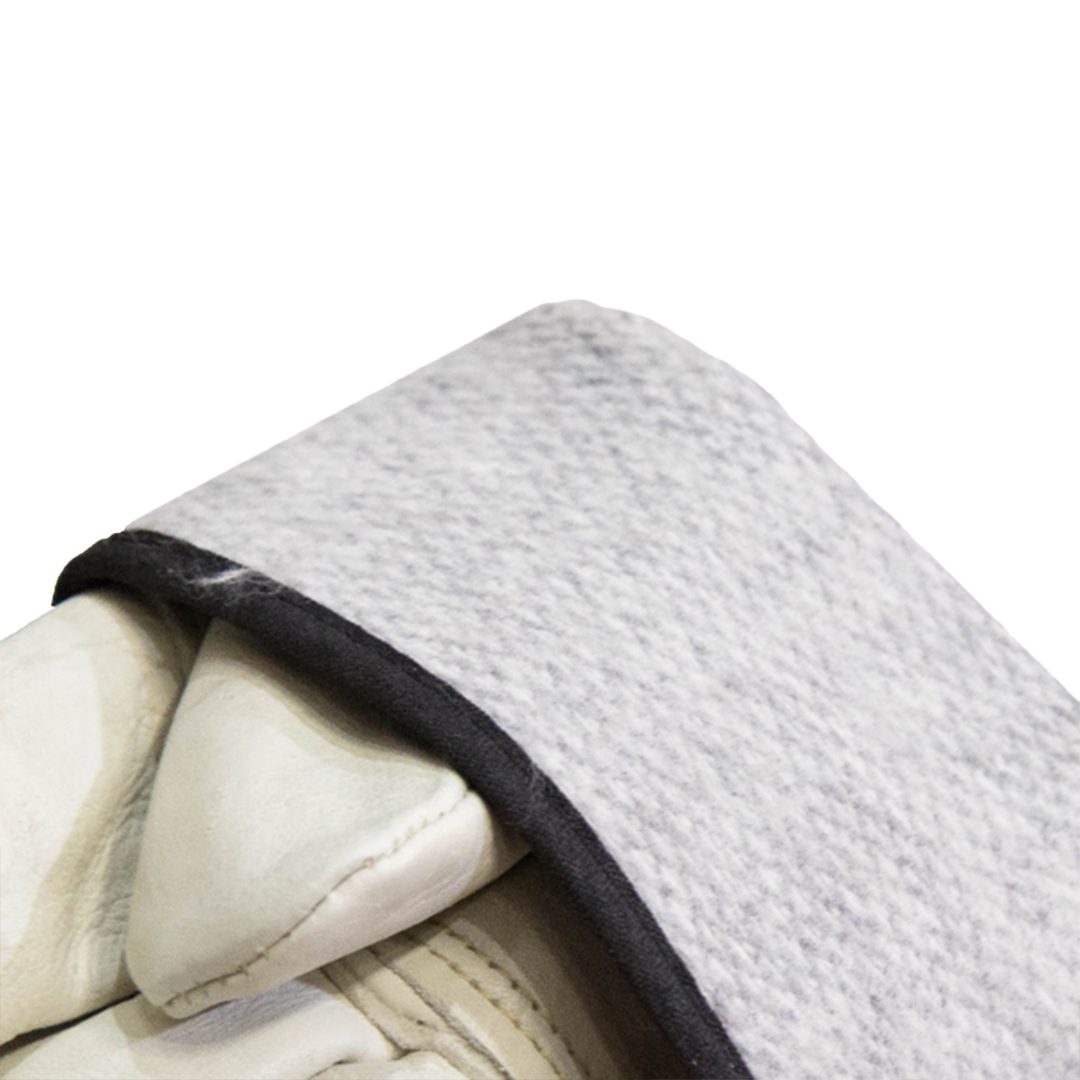
Membrane liners, moreover known as impermeable liners, are used for waterproofing safety gloves. In this method, a layer of waterproof membrane (plastic base) is inserted into the gloves to create a windbreak that prohibits the water drops from passing through. This helps alimony the hands well-appointed and dry in wet working conditions.
When it comes to safety work gloves, there are two wontedly used construction methods to unzip waterproofing gloves:


This triple-layer diamond is considered the most durable (i.e., less wear and tear) and breathable, but it is moreover increasingly plush to do when compared to other construction methods.
The way the membrane is fastened in between the two layers differs for variegated types of safety gloves.
- For leather and mechanics, the waterproofing membrane is inserted in between two layers. The inner layer is stitched with the outer layer without the stitches going through the membrane to stave puncturing and rabble-rousing it. A drawback of this technique is that considering there are three unshared layers, it can lead to slippage between materials which reduces the gloves’ sense of finger and dexterity.
- For string knit gloves, the waterproofing membrane is laminated in between the outer and inner layers. This process allows all three layers to unify as a single layer, so there is no slippage between any materials.
As once discussed earlier, liners can be widow (either sewn or inserted) to enhance mechanical protection. For example, leather gloves on their own don’t offer significant protection from cuts or punctures. Leather gloves that offer mechanical protection versus cuts and puncture have liners or inserts with these properties widow to them.
Similarly, liners can be widow into gloves to modernize repletion and sense of finger by using materials like cotton and nylon, or for structural support, as is the specimen in chemical gloves. You can refer to features and nature of chemical gloves under glove categorization to review this information again.
Glove treatments are a cost-effective way to introduce features in gloves that may otherwise be costly. Some of the most wontedly used treatments include:
There are spare features that can be incorporated into gloves to unzip increasingly specific features necessary for your work tasks or conditions.
- Finger caps: Crush resistant shell inside the tips of the fingers to help resist crushing. However, finger caps reduce the level of dexterity.
- Touchscreen: Powdered stat is incorporated into the palm coating to make safety gloves touchscreen compatible.
- High visibility (Hi-viz): Hi-viz shell or retro reflective strips (orange, green, or yellow) to enhance hand placement visibility and measure glove compliance.
- Non-marring: Marring is the effect of leaving overdue residue/markings without touching a product, like fingerprints on a glass. Non-marring gloves are platonic for quality tenancy for finished products.
- Dotted palms: dotted palms help modernize grip, but only marginally.
- Back-of-hand impact protection can be sewn or molded into gloves to protect workers’ hands from injuries. It is rated on a scale of 0-3, with level 3 offering the highest level of impact protection. Thermoplastic rubber (TPR) is the most popular material used for back-of-hand impact protection. Superior Glove and some other manufacturers use a proprietary tousle of materials to unzip higher levels.
In wing to the glove specific considerations we’ve discussed above, there are other, equally important, factors to alimony in mind when choosing safety gloves to ensure wearability, cost-effectiveness, comfort, and other factors that determine successful adoption. These include:
- Glove sizing
- Glove Laundering
- Hand protection nomenclature for workplace hazards

Glove fit is crucial in determining its wearability and hazard protection. If the gloves are too small, it can restrict movement of the hands and discourage workers from wearing them. Similarly, loose gloves can slip off at the slightest movement and make handling tasks difficult. In either case, the wearer is exposed to risk of serious injury.
There are two measurements that determine the size of gloves:
- Distance virtually your knuckles
- Overall length of your gloves (palm to fingertips).
And there are ways to identify if your gloves fit poorly:
- Overall finger length—if the finger crotch does not fit to the wiring of your fingers, or if you have glut material on the fingertips, this indicates you should size up or size down, respectively.
- The palm—if the glove’s palm doesn’t imbricate your palm fully, this indicates that your gloves are too small and you should size up.
- Excess material—excess material virtually your hands or bunching in your palms when you tropical your hands indicates that the gloves are oversized. This ways you should size down.
Measure your hands and refer to the orchestration unelevated to find your platonic glove size.
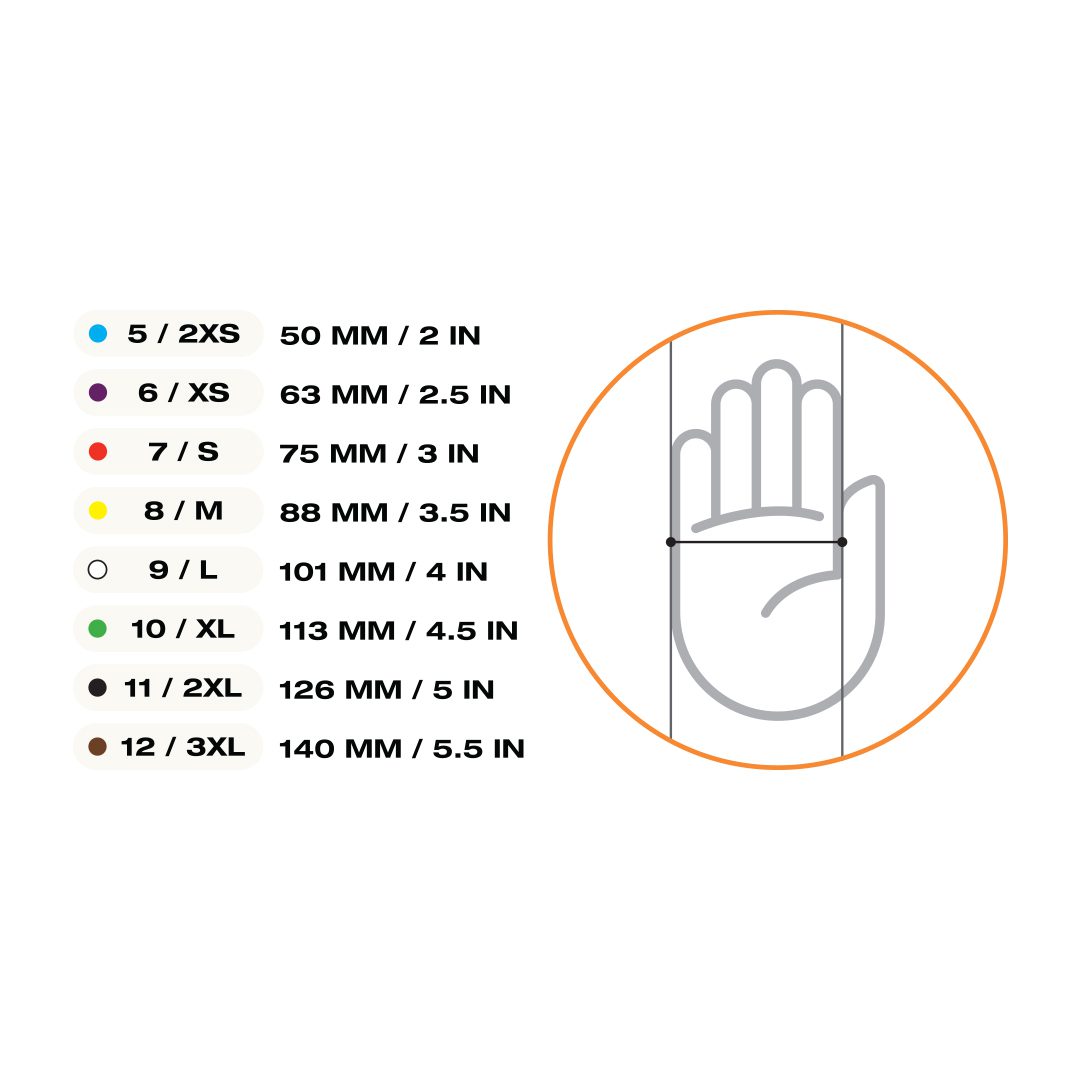

Laundering gloves can help in saving costs. Gloves made from high-quality materials can be laundered to increase their wear life without impeding performance.
Read on to learn some vital considerations to alimony in mind when laundering gloves.
Ideally, leather gloves should be dry cleaned.
If you plan to wash your leather gloves at home, you will want to use a leather workout soap that will replenish the oils when into gloves.
- Wash in hot water (170°F/75°F)
- Tumble dry upper heat (155°F/70°C)
- No bleach
When washing gloves made with para-aramid materials, stave using bleach at all costs. Using bleach will forfeiture the glove scrutinizingly immediately. Also, long exposure to UV light weakens the material and shortens the glove’s lifespan. Therefore, para-aramid gloves should not be kept under uncontrived sunlight for too long when drying.
- Wash in warm water (105°F/40°C)
- Tumble dry on medium to low heat
HPPE, nylon, and polyester are thermoplastic materials, which ways they can melt when exposed to heat. When laundering gloves made of these materials, ensure that you do not wash them in hot water. You can use regular detergents and bleach, but not upper or sanitation heat.
- Wash in unprepossessed water ((85°F/30°C)
- Tumble dry on low or no heat
The only consideration to alimony in mind when laundering gloves made with cotton materials is the risk of shrinkage. For this reason, while you can use regular detergents and bleach for cotton gloves, stave using upper or sanitation heat.

Not all safety gloves protect equally. Gloves designed for one type of hazard may not sufficiently to protect versus another, plane though they may squint similar. And the nature of the hazard will stupefy the selection of your gloves.
So, how do you determine which gloves offer the right level of protection for your worker?
To solve this problem, industry standards were established that refer to specific test methods to assign protection levels for safety gloves, including cut, impact, puncture, arc flash, heat, flame, vibration, abrasion, cold, and chemical. These standards were introduced to create a worldwide language for safety managers, distributors, and manufacturers to pinpoint protection levels and be held subject for their claims.
Industry standards that govern protection levels for workplace hazards include:
- In North America, the ANSI/ISEA 105-2016 and ANSI/ISEA 138-2019 North American Standard
- In Europe, the EN388 European Standard (CE)
- In UK, UK Standard (UKCA)—developed when the UK split from the EU
- NFPA 2112 (The National Fire Protection Agency Standard)
The ANSI standard specifies the nomenclature and testing requirements for hand protection. They then refer the test methods as per the ASTM (American Society for Testing and Materials) or EN (European Standard) test methods to assign protection levels for safety gloves. This nomenclature can squire users in the selection of gloves for specific workplace hazards.
Check out the table unelevated for a quick summary of the ANSI safety standards for protective gloves versus hazards, including cut, impact, puncture, heat, abrasion, dexterity, and vibration.
Hazards
Icon
ANSI Ratings/levels (lowest to highest)
Cut

ANSI/ISEA 105 (A1 – A9)
Impact

ANSI/ISEA 138 (1 – 3)
Puncture (Probe)

ANSI/ISEA 105 (1 – 5)
Puncture (Hypodermic Needle)
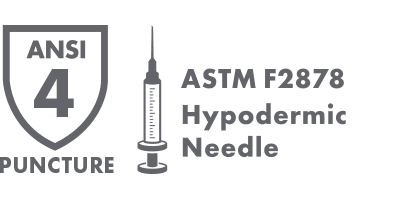
ANSI/ISEA 105 (1 – 5)
Heat

ANSI/ISEA 105 (1 – 5)
Abrasion

ANSI/ISEA 105 (1 – 6)
Vibration
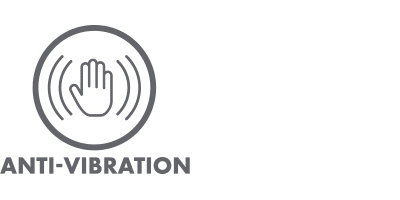
ANSI/ISEA 105 (Pass or Fail)
The CE-EN388 is a mandatory European standard that dictates the testing methods and performance ranges for gloves that provide protection versus mechanical hazards, including abrasion, cut, tear, puncture, cut (TDM test), impact, and cold.
Check out the table unelevated for a quick reference of the EN388 safety standards for protective gloves and the score marking under the EN388 shields.
Hazards
Ratings
Abrasion Resistance
1 – 4
Cut Resistance – Coup Test
1 – 5
Tear Resistance
1 – 4
Puncture Resistance
1 – 4
Cut Resistance, TDM Test
A – F
Impact Protection
P, F, X

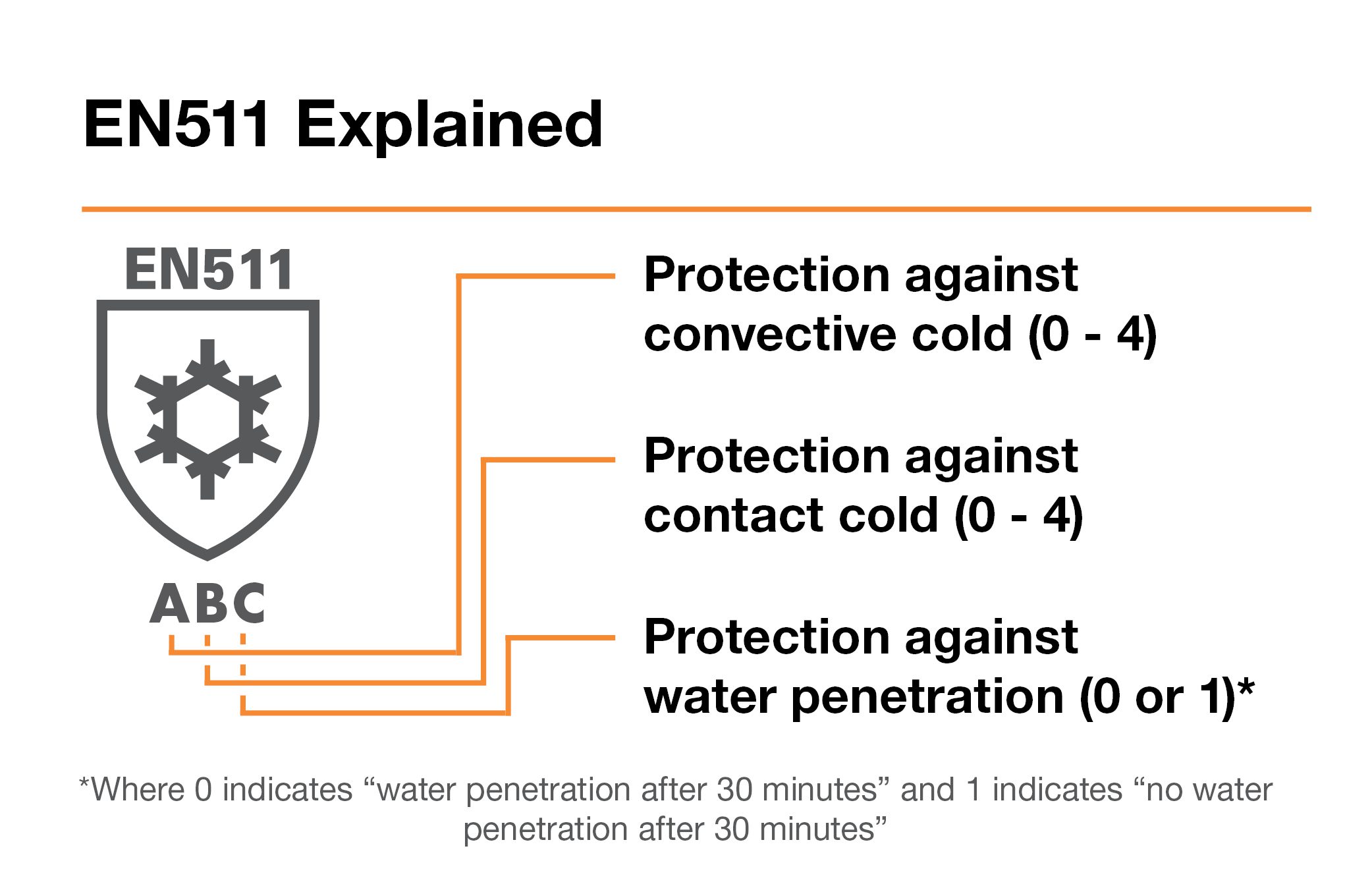
The CE-EN388 is a mandatory European standard that dictates the testing methods and performance ranges for gloves that provide protection versus mechanical hazards, including abrasion, cut, tear, puncture, cut (TDM test), impact, and cold.
Check out the table unelevated for a quick reference of the EN388 safety standards for protective gloves and the score marking under the EN388 shields.
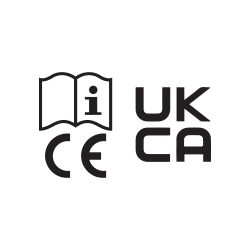
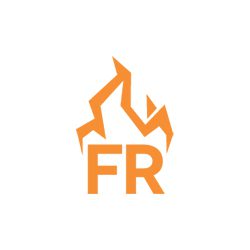
The National Fire Protection Agency (NFPA) 2112 standard establishes the minimum requirements for the design, construction, performance, evaluation, certification, and testing methods for the manufacturing flame-resistant (FR) PPE used in areas at risk from short-duration thermal exposure from fire.
NFPA 2112 was originally established for FR garments. In the most recent edition in 2018, testing standards were moreover extended to include hand protection, whereby gloves manufactured in compliance with the standard provide protection versus wink fires to the wearer’s hands and wrist.
NFPA 2112 compliant gloves are identified by the pursuit marking:
By now, you should have a clearer understating of what goes into manufacturing safety gloves, its meaning, and the complementary features and nature that influence their performance. However, glove knowledge does not end here. The next step is to learn well-nigh gloves designed for various hazards and how these gloves protect the wearer by counteracting the underlying forces that lead to injury. To learn this, and more, stay tuned for updates on our resource page for new and upcoming posts.
The post Glove 101 appeared first on Superior Glove.